top of page

Shape Your Career With The
ANSYS COURSE IN COIMBATORE
Ansys Course Details in Coimbatore
In Coimbatore, ANSYS courses typically cover finite element analysis (FEA), computational fluid dynamics (CFD), and electromagnetics simulations. These courses delve into software tools like ANSYS Mechanical, Fluent, and Maxwell for engineering analysis and simulation. They equip participants with skills in structural analysis, fluid flow simulation, heat transfer, and electromagnetic modeling. Taught by experienced professionals, these courses often include hands-on training, case studies, and practical applications to enhance understanding. Participants gain proficiency in utilizing ANSYS software for solving real-world engineering problems, making them valuable assets in industries ranging from automotive and aerospace to electronics and manufacturing.
23,564 Total Students
4.9
(12559 Rating)
183 Reviews
What will you learning outcomes in Ansys Course in Coimbatore
-
Fundamentals of finite element analysis (FEA) and computational fluid dynamics (CFD).
-
How to use ANSYS software tools for structural analysis, fluid flow simulation, and electromagnetics modeling.
-
Techniques for meshing, solving, and post-processing simulation results.
-
Practical applications of ANSYS in engineering design, optimization, and problem-solving.
-
Skills for conducting simulations related to heat transfer, stress analysis, fluid dynamics, and electromagnetic fields.
-
Hands-on experience through case studies, projects, and real-world examples.
-
Problem-solving strategies and best practices for efficient use of ANSYS tools.
-
Collaboration and teamwork in multidisciplinary engineering projects.
-
Theoretical background and practical implementation of simulation techniques.
-
Insight into industry standards and practices for using ANSYS in various engineering sectors.
Requirements for Ansys Course in Coimbatore
-
Basic understanding of engineering principles and mathematics.
-
Familiarity with computer-aided design (CAD) software would be beneficial.
-
Access to a computer with ANSYS software installed (often provided by the training institute).
-
Adequate hardware specifications to run ANSYS software smoothly (e.g., sufficient RAM, processor speed).
-
Willingness to learn and actively participate in hands-on exercises and projects.
-
Good analytical and problem-solving skills.
-
Strong commitment to attending classes and completing assignments.
-
Background knowledge in relevant engineering disciplines such as mechanical, civil, aerospace, or electrical engineering.
-
Some courses may have prerequisites, so checking with the training provider for specific requirements is advisable.
-
Fluent understanding of English, as courses may be conducted in English.
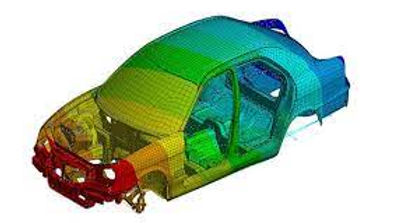
Ansys Course
Duration
1 Months
Lessons
8 Modules
Languages
Tamil & English
Certificate
Yes
Software Covered
1
bottom of page